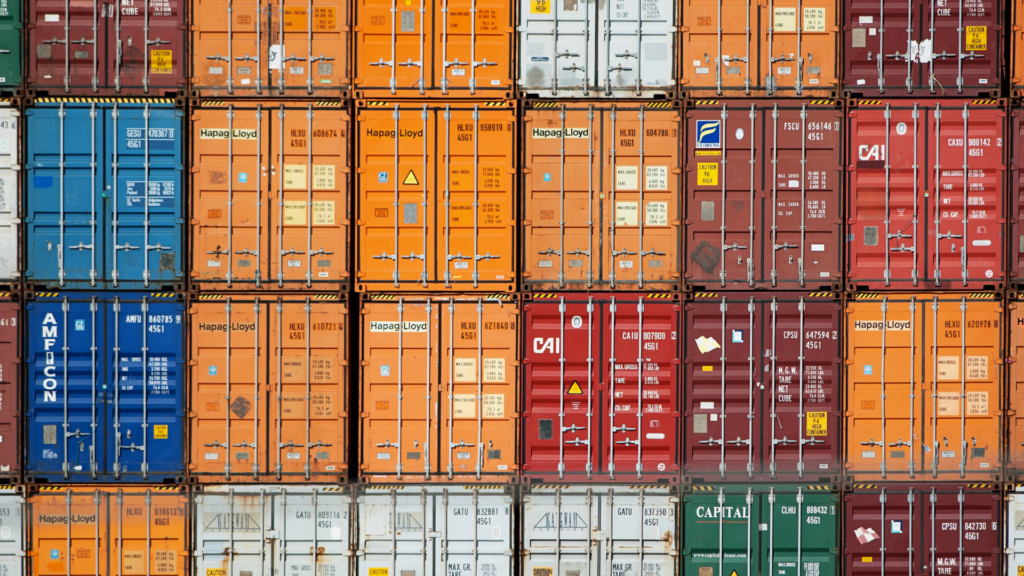
Introduction
Fire safety on container shipping has, for various reasons, and predominantly due to the sheer capacity, become compromised. Existing applicable codes have become effective only on occasion that an incident is small and that all code criteria and prescribed procedures go to plan. The result is that there is little or no margin for error.
Placing a level of fire safety firmly at the CTU itself will be a major contribution to the existing raft of requirements, will enhance safety at all points in the logistical chain of container transport and provide essential relief to a system that is now, on all but the smaller vessels, at and beyond the very limit of effective fire safety. It may also allow further innovation and increased capacity.
The standardised shipping container, or Cargo Transport Unit CTU), has remained unchanged since its inception 70 years ago. Over 90% are for general purpose (dry freight). They are made from rust-resistant Corten steel and must be ‘Spray-tight’. ISO standard 668:2020 applies. That code details the construction, markings, fittings and other provisions. The code makes no provisions for fire safety.
The dimensions and fittings are effectively set in stone because an entire industry and infrastructure has developed around them. Therefore, any alterations and ‘next generation’ changes must be fully compatible with that infrastructure. This does not preclude other changes to the code or voluntary adaptations. The Customs Convention on Containers encourages innovation.
The fundamental criteria of fire safety includes:
- Prevention
- Fire resistance
- Compartmentation
- Alert
- Escape
- Fire Fighting
- Fire Fighting Access
The fundamental aims of fire risk assessment are to:
- Identify and remove or reduce ignition sources
- Mitigate the effects of any remaining ignition risk
- Remove or reduce all sources of combustible material
- Protect all remaining combustible material or risk
The remaining fire risk should then be As Low As Reasonably Practicable (ALARP) and the priority of actions needed to achieve this will be graded in terms of;
- Immediate: To address any item that is a clear and present danger such as blocked fire escape routes and fire door wedges.
- High priority: To address items that require urgent action and attention such as damaged fire door closers.
- Medium priority: To address items that cannot be fixed rapidly such as excessive fire door gaps.
- Low priority: To enable long term solutions that require substantial funding or redesign.
The CTU was entirely fit for purpose at inception and for many years after. In itself, it did not present a fire risk such that it required any immediate attention to structure or design. Its primary purpose was of freight security and uniformity of handling from supplier to consignee.
It was surmised then, and remains true today, that a small fire in a CTU, involving ordinary cellulosic combustible materials, will often self-extinguish due to lack of oxygen. A fire could otherwise be contained and isolated to that container because there was reasonable access to most sides and to the doors. However, the industry around it, in the marine environment in particular, has seen it become extremely crowded in stacks that are inaccessible for any effective or timely emergency action.
Most fires still do not breach the CTU but for those few fires that do, or that are caused by a particular fire trend of rapid growth, each CTU is now a fire risk to the others. As in any fire situation where direct firefighting action cannot be quickly brought to bear, fire spread to CTUs above and besides, if not covered by any full-flood fixed installation, will grow exponentially. That risk is now present and has been so for many years, particularly in deck cargo, and must be addressed. Under deck the cargo space has air-sampling fire detection and associated fire fighting system. There is early detection, alarm and response. On deck there is only manual patrol and most of the cargo is out of site of the bridge.
Solutions
The most effective and reliable fire protection is by passive means. This is achieved by construction, materials, fittings and coatings that have a long ‘shelf-life’, require little maintenance or monitoring and no human activity in the event of fire. This would include, for example; fire resistance, compartmentation and dampers.
Active fire protection methods are secondary and complementary but by no means inferior. This would include, for example; fire suppression systems or appliances and door closers.
Fire detection may be regarded as both passive and active since it a permanent fixture but requires some human interaction or greater monitoring and maintenance.
This article will consider various potential avenues of passive and active fire protection for the CTU. It is true to say that 100% fire safety is not achievable. So-called ‘Gold’ standards are usually prohibitively expensive and often not compatible with business viability. However, there will always be fire and there will sometimes be exceptional fire situations and unpredictable trends. The minimum design standard of fire protection adopted for any risk must be based upon all reasonably expected fire events. Fire codes are premised upon that understanding. It is accepted that deliberate fire setting, sabotage and terrorism cannot be combatted by general design and code. However, where there are known and credible threats of such nature, the affected industry must consider further measures.
As stated earlier, fire protection aims to reduce the risk to As Low As Reasonably Practicable (ALARP). In this respect, the staging of improved fire safety proposals by short, medium and long-term criteria is the best approach. Each stage will contribute to safety and reduce fire losses but it is an important financial imperative that intermediate steps are not rendered redundant by longer term step. They should remain valid throughout the process and serve as building blocks of safety.
These suggestions must never be sought to justify any reduction to existing safety standards, practice and codes. They are an enhancement to existing provisions and are now necessary in order to support those existing provisions which have been shown in many cases to be lacking or at least only just adequate.
Short term
Short term solutions are ideally cost effective by way of materials and manpower. They also should be capable of implementation widely and voluntarily. The following suggestions are in this category. They are presented in order of preference. Each will then complement others to provide a level of safety such that some of the medium and long-term solutions may be rendered unnecessary.
1. Intumescent mesh
At present, the most vulnerable component of the CTU is the timber or bamboo flooring. Fire spreads upwards and outwards. When a fire erupts from a CTU, ships fitting or other event in close proximity to any CTU, the heat will come to bear on the undersides of any unit above the fire. The gaps between stacked or tiered units create ideal ventilation conditions for fire travel between them and the floorings will be dry.
When this stage of fire attack is reached it will not be possible to direct water directly at all of the underfloor. Boundary cooling from afar and above will be almost entirely deflected by the upper steel structure of the units. Fire then develops unhindered at the underfloor and penetrates the interior via the flooring panel joints and edges. The result is a further container fire and the fire begins its spread to other units in time. That time becomes rapidly and exponentially accelerated as more containers become similarly involved.
An intumescent barrier (a coating or covering which forms a charred swell when heated, thus protecting the material underneath) over all of the underside of flooring timber will prevent and delay all but the most extreme and prolonged fire attack through the flooring.

Container (CTU) fire safety – Time for change

About the author:
David Townsend is the Principal Fire and Explosion Investigator with Andrew Moore and Associates (AMA). He has served the fire industry for 45 years the last 25 of which has been dedicated to fire investigation.
David served a full 30-year career in the London Fire Brigade the last 11 of which was in fire investigation. As an investigator in the private sector since 2006, he soon became involved in substantial marine casework worldwide.
The mesh construction, as opposed to paint or spray products, will allow the timber to breathe. It is ‘cut-to-fit’. It can be quickly stapled or tacked to the underside including of individual replacement boards.
It remains fit for purpose for as long as the timber upon which it is fixed. It is easily repaired if damaged or torn and is environmentally robust. It can be re-used.
The cost of materials is around US$1500 per TEU. With bulk order that figure is likely to be substantially reduced. The cost of a new TEU is US$3500. Whilst this represents a high relative additional cost, the benefits and investment are considerable.

The mesh would be attached to the flooring boards before fitting to the CTU. A small over-lap at the edges will prevent gaps in the mesh and provide a fire-stop function at the floor edges joining the steel structure.
Conducted heat through the steel floor structure and forklift guides would also be resisted.
Steel flooring can be coated with intumescent paint if desired. This will delay the buckling of the flooring from heat attack but the timber flooring is the most important item for this application.
The Intumescent coatings and products industry is constantly developing through research and development. The recruitment of an industry partner will likely provide a suitable and cost-effective bespoke solution.
2. Non-combustible fire break
Many CTUs contain almost entirely non-combustible goods. The only combustible contents will be the packing, dunnage, pallets and some components. These shipments (metals, machinery, most building materials, stone etc.) will not require a scientific analysis to reliably declare to be non-combustible. If a fire should arise in such CTU (for example by dropped cigarette at packing and pallets) then it is likely that the packaging and pallets, being cellulosic and not of great quantity, will self-extinguish or reduce to smouldering.
CTUs with non-combustible goods, if fully occupying the centre two or three rows in a bay will effectively act as a lengthways fire break at midships. This will significantly slow fire development from an origin either side. This is a tactic that can be applied to both hold and deck stowage. This will also make fire response and targeted discharge of involved containers easier.
Logistically, this would complicate the bay planning. However, it would be relatively easy to build this proviso into the software. It is also clearly applicable only to the larger vessels with greater than, say, nine-row holds.
3. Solar reflective paint
The ambient, incidental heating by the sun of CTUs during transit and at rest in Terminals has a bearing on many chemical substances but also may affect quality and performance of other freight. The internal temperature is currently controlled only by the incidental colour of the outer surface paint. Light colours reflect more light than dark colours and the unit remains cooler inside. Maximum temperatures may, in some climates, raise temperatures near to levels considered, in some products, to be critical.
2014 research by Xerox entitled ‘Are Ocean Freight Containers Safe For My Product?’ states:
that the majority of the temperature and humidity fluctuation occurs during the inland transport process, and not during oceanic transport. For example, the temperature of a freight container during summer months may reach 57C (135F), but the actual oceanic temperature fluctuation during oceanic transport does not surpass 26C (80F).
If the CTU exterior top and sides are coated in a solar-reflective paint the internal temperature will always be substantially lower in comparison to a standard CTU but also, the temperature will not fluctuate as greatly. The risk of reaching critical internal temperature ranges will be eliminated or at least be significantly reduced (an additional benefit to reefer containers will be a reduction in energy use).
Container sweating or ‘rain’ is a consequence of extreme temperature fluctuations. The use of solar-reflective paint, by reducing the temperature fluctuation range, will also reduce container sweating.
The paint is entirely suitable for the application proposed and can be produced in colours to suit branding if required. It will not be compromised by application of standard signage and insignia. Dependent upon type, application and quality, it will reduce the internal temperature by about 20%. The cost is around US$13 per m² (approx. US$700 per TEU) but it is not additional to the finish coat.
Medium term
Medium term solutions will often involve greater investment in equipment and manpower. They will also require some retro fitting work (brackets and protective cages etc.) to the container steel. However, they should still be capable of instigation and application to all existing CTUs.
1. Fixed single use, heat activated, dry powder fire extinguisher
The principal operation of this device is not innovative. Many warehouse buildings and other industries use them to cover a specific risk point. The innovation now is that the product has been developed such that it is smaller and easy to place. It has a five, or more, year shelf life.
Its use would have two functions; firstly, to provide automatic control or extinguishment of a developing fire in the CTU. Secondly, when placed at the rear, to extinguish or control an external fire that may have penetrated the door seal or the flooring at the doors (these are relatively common findings).
A limitation for this installation is that there would need to be at least two units per TEU. However, it opens the field to specific fire protection industry development to provide a bespoke system for retro-fitting to existing CTUs.
The cost per ball-type is as little as US$20. Fitting will be the dominant cost factor.
2. Gas detection
Early alarm of fire is the first fire safety principle after prevention. Fire detection is achieved by device sensitivity to (or combination of) smoke particles, flame propagation, heat, ultra violet ray (flame), infra-red ray (heat), visible smoke (cctv), or combustion gases.
The sensitivity and type of device required is governed by the risk covered and construction factors. In respect of CTUs the most efficient and cost-effective method would be the detection of Carbon Monoxide gas (CO). The CO detector is compact and will require only one per CTU (20’ or 40’). This will render it suitable to be placed at the top front of the CTU and thus adequately protected from damage when loading.
CO is an ambient gas and will be distributed reasonably quickly throughout the CTU. The CO alarm will detect slow smouldering fire faster than any smoke or heat detector.
Whatever detection system used can and must be linked remotely to the ships BMS in the same manner as temperature monitors in Reefers.
The cost of a single point, independent CO detector for domestic use is around US$100. The more dominant cost will be that of fitting and connectivity to ships SMS or to a cloud service. Due to the steel ship and CTU structure, signal transmission to SMS is the main limitation but it is achievable. This is a good example of where marine and non-marine industry innovation and cooperation will prove beneficial. It requires very basic research and development. Some buildings already have multiple, very cheap, environmental sensors with total BMS connectivity and remote monitoring.
Long term
Long term solutions are those that will require some redesign of the CTU or further fittings made at the point of construction or refurbishment.
1. Break out panels
At present there is no means to quickly create an opening in any part of a CTU in order to project a water jet or to spray directly inside. Angle-grinder cutting, Hydro Pen (commercial product) and lance are all manpower and time intensive. They also require the operative to remain near to the burning unit for too long and, due to heights, lashings and access, will not be capable of use at all tiers and bays.
A clearly labelled break-out panel could be created at the top of each door and at the front panel that requires only a sledge hammer to breach. Water can then be directed into the opening from a safe distance or a hose branch placed inside and lashed (a lashing ring should be provided above the panel opening). This would be subject to some of the similar limitations as the Hydro Pen but far fewer.
2. Fire resistant side
If all CTUs were constructed with one side only having a 30-to-60-minute fire resistance then, provided the entire row is correctly oriented front to forward, each row will have a short duration fire division. This will effectively compartment the space.
This will not be a continuous barrier in the same sense as is applied to buildings and the principal will require considerable research and testing.
Logistically, this would complicate the bay planning. However, it would be relatively easy to build this proviso into the software. Colour-coding would provide a visual guide and assist to loading stevedores.
3. Fixed water mist bars
The fitting of a square, open-holed bar alongside or below the top rail with a ships hose coupling at each end would allow fast application of water mist into the CTU. Each end would require a non-return valve and the coupling ends may need to be recessed to avoid damage to fittings in normal container operations.
A difficulty would be the access to high tiers on deck and to those in the hold whose access will be obstructed due to the hold construction.
4. Special DG
See Fixed CO2 and Pressure venting below.
5. Fixed CO2 or powder
In the same way that Reefer Units and gas or flammable liquid container units are specialised, a further category should be considered with built-in detection and fixed, firefighting installation.
6. Pressure venting roof
When an explosive, or rapid conflagration state is reached in a CTU the resulting explosion is significantly magnified due to the container being a virtually sealed unit. This is the operating principle of explosive fireworks, grenades and pipe bombs.
In industrial property that carries a risk of explosion there will be provision of explosion vents; weak spots in the construction that will give way and dilute the power of the explosion or pressure wave.
If the roof of a CTU were to have an inherent weakness then it will be the point of bursting. Burning debris may be less likely to be expelled. Inherent explosion relief provides some degree of control and predictability of events that may steer firefighting tactics.
7. High pressure, rapid intervention hose reel
This is not a solution directly applicable to the CTU. It is a ship’s fitting. It is important that this is highlighted because ship’s hydrants and hoses have remained largely unchanged. One consequence of the increased size of vessels is that the CTU has become more distant from the fire fighting water source.
Public fire services have, for many years, used a high-pressure hose reel system on appliances. Hose reels are rapid deployment and lightweight equipment that provide fast response. They are robust and low maintenance. When enhanced by a high-pressure water supply the effective and efficient use of water is impressive. The system can also be enhanced by practical accessories and remote connectivity to key areas via fixed pipework.
The main hardware is of 100m lengths of hose with permanent branch on fixed drums that need not be fully run out before charging. The quantity and locations will be determined by the individual systems and ships construction but one drum per bay would be logical.
The system would be charged by the fire pump as at present but would require a booster for high pressure. Booster pumps are already installed on ultra large container ships with high level monitors.
Conclusion
The container industry is fully established, reasonably well regulated and relatively incident free (in term of mileage per CTU). The capacity of container ships has rapidly increased but the infrastructure around those vessels has not kept pace. It is also a fact that shoreside developments will increase the density of shoreside CTU storage. Fire risk assessment aboard and ashore require a fundamental review.
The premise of this paper is that, by applying fire safety provisions now to the CTU itself (which has never been done) the risk assessment of the industry as a whole can be brought up to date and greatly enhanced such that further development will be possible without radical change.
Any solution involving fittings and alteration to a CTU must take account of the realistic and practical use of the CTU. It must be as robust as the CTU. If it presents a vulnerability then it’s use and purpose will be negated.
At present, the risk now presented above deck is comparable to a high-bay warehouse without a building envelope. If a building were to be constructed and intended to be filled with CTUs to a height of 30m and a footprint near to the area of a sports field it would be required to be built to and fitted with considerable fire safety provisions. If that building included no means of escape for occupants to a place of ultimate safety then the building would not exist.
Cost will always be a factor. Proposals with long life that are virtually free of service and maintenance will have an inherent long-term value that will, in time, negate the initial cost of installation. The life and value losses saved by effective fire prevention are significant but, unfortunately, are not reliably calculable.
Practicability must also apply; the intumescent mesh, for example, would be totally inappropriate if CTU undersides were subject to regular impact or interference in normal use.
There will never be a final solution. Fire risk assessments are dynamic. They must be subject to constant review. By providing now a CTU-level of fire safety all future fire risk assessments are enhanced and future fire trends will be better handled.
The capacity on container ships at which critical safety factors became compromised is debatable. Many mariners, as found by an audience survey at the 2021 International Safety@Sea Week, believe that figure was reached at 10,000 TEU capacity. However, there now exists 400m, ‘A’ Class vessels (23,992TEU). On one such vessel the centre deck cargo forms an undivided mass of FEUs stacked eleven (tiers) high, twenty-four (rows) wide and thirteen (bays) long. The above mass sits between the only fire breaks; the engine room housing and the accommodation block, both of which, it can be assumed, are protected by a drencher system with independent fire mains supply.
On that vessel there appears to be a single, high-level monitor at the forepeak, no intermediate high-level monitors and no high-level monitor aft. Tween-bay gantries reach only to tier 92. The monitor output of fire tugs will be barely able to reach the top of the load and the throw is unlikely to be capable of covering a whole bay from one side only.
It is not implied that there is any fault with this vessel. It serves only as an example of the current vessels of that class. A severe cargo fire on such vessel being capable of reasonable control at sea or at port without there being substantial aspects of the above listed CTU fire protection installed, cannot be envisaged.
It is common knowledge that large, burning fire debris can be projected by during-fire explosive events above and to either side of a vessel to a distance equivalent to the ship’s length. We also know that an entire vessel and cargo can become involved that, at port, presents a high radiant heat risk. In both scenarios, if a larger vessel is involved in like manner, neither the ship, salvage tugs nor the port fire services will be adequate (this is not a criticism of these services).
There has been an increase in CTUs aboard larger ships becoming loose and dislodged in high seas. One such recent incident resulted directly in fire. Fortunately, the ship was at anchor and assessable by tug. The fire was contained to a single bay. If at sea, one must question if the ship may have been lost. Whilst this may be seen as a lashings issue (an element of the infrastructure that also appears to have remained unresponsive to the increased ship sizes), The fact of unprotected bay to bay fire spread on deck remains.
Fires in cargo will always arise. When they do so then, in order for ships systems, first responders and shore services to be effective, systems must be in place to limit the spread of fire. The CTU is the first line of that defence yet it currently has no provisions at all.
Organised and effective fire fighting and fire safety were both born at sea. A ship always needed to be self-sufficient for any journey duration. Cargo priorities and costs have negated the potential for a vessel to maintain that self-sufficiency status. Many need to call for external assistance and many are lost. This is not an issue unique to the container sector.
Self-Sufficiency requires that no reasonably expected fire should ever become uncontrolled and uncontained. In the container sector, the provision of a level of fire safety at the CTU will be a major contribution to reliably meeting that standard.
Note: This article was written by the author and published by the Standard Club.